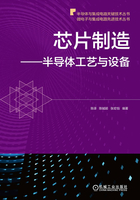
2.2.3 集成电路生产线的工艺设计
集成电路产品主要分为数字电路和模拟电路两大类。由于产品的品种和技术要求不同,因此需要不同的生产工艺。从线宽来区分,从较早的5μm到最新的7nm以下工艺;从加工衬底直径来区分,主要有150mm、200mm、300mm以及未来的450mm。工程投资金额存在数千万美元至数十亿美元的差异,洁净室面积也从数百平方米到数万平方米不等,因此选择适合的工艺技术及配套设备是工厂设计的基础。工艺设计应按集成电路生产线的产品类型、每月最大产能、生产制造周期、投资金额、长期发展进程等因素确定生产的工艺技术和配套的设备。对于线宽在0.13μm及以上工艺的集成电路的研发和生产,宜采用150mm或200mm生产线。对于线宽在90nm及以下工艺的集成电路的研发和生产,宜采用300mm生产线。集成电路芯片的生产工艺十分复杂,工艺步骤可高达千步以上,譬如:前段工艺用于形成集成电路中的有源器件及无源元件,包括清洗、薄膜、光刻、刻蚀、离子注入等工序。后段工艺用于完成电路中元器件之间的连接及形成保护层等,包括光刻、刻蚀、清洗、金属化、化学机械抛光等工序。进入后段工艺的硅片应避免与前段工艺混用设备,以免金属离子等污染前段工艺中的硅片,造成电气性能异常。
150mm生产线通常采用的是敞开式生产方式,操作区空气中的尘埃会直接影响晶圆片电路的电气性能,因此对操作区的洁净度要求较高。为了节省运行费用,保证洁净度要求,通常采用壁板将操作区与低洁净度要求的设备区分开。随着芯片加工尺寸向200mm及300mm发展,对于加工线宽的要求也越来越高,大面积高洁净度的洁净区的造价和运行成本越发昂贵,因此采用标准机械接口(Standard Mechanical Interface,SMIF)加微环境的生产方式成为200mm及300mm生产线的主流生产方式。对于早期的200mm生产线来说,大部分晶圆片的传送、存储和分发是通过人工操作完成的。目前多数200mm和300mm生产线设有自动化物料搬运系统(Automated Material Handing System,AMHS),其优点在于能够有效地利用洁净室空间、有效地管理生产中的芯片、有效地降低操作人员的负担,进而减少在传送晶圆片时的失误。在一些300mm生产线,运输系统可延伸到不同的生产区域,借助吊挂传输系统(Overhead Hoist Transfer,OHT),将芯片直接传递到设备端。未来AMHS系统还要在提高生产速度、缩短生产周期和快速适应芯片制造环境变化等方面进行持续改善,以适应和满足芯片工厂的各种需求[1]。
随着集成电路芯片制造技术的发展,对应的封装技术也发展得十分迅速。封装不仅起到集成电路芯片内键合点与外部进行电气连接的作用,也为集成电路芯片起到机械或环境保护的作用,从而使集成电路芯片能够发挥正常的功能并保证其具有高稳定性和可靠性。
20世纪80年代之前的主要封装形式为通孔插装,以TO型封装和双列直插封装为代表,主要的工艺流程包括中测、减薄、划片、粘片、包封、切筋成型、电镀、打标、测试、包装等。20世纪90年代后,球栅阵列封装和芯片尺寸封装发展迅速,主要的工艺流程包括中测、减薄、划片、粘片、清洗、塑封、装配、回流焊、打标、测试、包装等,主要特点是缩小了引脚间距并采用底部安装引脚的形式,大大促进了安装技术的进步和生产效率的提高。20世纪90年代末,封装技术进入了三维堆叠封装时代。通过在垂直方向上将多层平面器件堆叠起来,并采用硅通孔技术在垂直方向实现通孔互连的系统级集成,可以减小封装的尺寸和质量。还可以将不同的技术集成在同一封装中,缩短互连导线的长度从而加快信号传递速度,降低寄生效应和功耗。近年来三维堆叠封装得到了较快的发展,主要的工艺流程包括涂覆、光刻、溅射、再涂覆、电镀、回流焊、测试、打标、包装等。