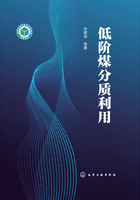
2.2 低阶煤中低温热解典型工艺
至目前为止,国内外研究开发出了多种各具特色的煤热解工艺方法,有的处于实验室研究阶段,有的进入中试试验阶段或工业化示范阶段,也有的达到了工业化生产阶段。按传热方式的不同分为内热式、外热式、内外混合式热解技术,按热载体的不同分为气体热载体、固体热载体和气固热载体热解技术。
按照粒度划分,国内外主要的已有装置的热解技术见表2-6。块煤热解技术已经工业化应用,小粒径煤和粉煤热解技术多处于工业化试验或示范阶段。典型的块煤热解代表工艺主要有鲁奇(Luigi)炉、考伯斯(Koppers)炉、SJ炉;小粒煤热解技术主要有LFC/LCC、CGPS、SM-GF、天元回转窑、龙城旋转床、内构件移动床;粉煤热解技术主要有DG、ZD、煤拔头、SM-SP、输送床粉煤快速热解、日本快速热解。小粒径煤和粉煤热解技术工程化问题尚未完全突破,成为行业研究的热点。
表2-6 典型的热解技术汇总

按照反应器类型粉,热解技术的分类及典型工艺如下。
2.2.1 移动床热解工艺
2.2.1.1 SJ低温干馏技术
国内在鲁奇三段炉的基础上,开发设计了不同类型的内热立式干馏炉,各种炉型结构基本相同。国内典型炉型和工艺有:陕西神木三江煤化工有限责任公司SJ系列和陕西冶金设计研究院的SH系列、中钢鞍山热能院ZNZL3082型、原化学工业第二设计院MHM型直立炉,以此为基础在榆林已形成块煤年产5000万吨兰炭产能。
在我国对鲁奇三段炉的改造设计中,SJ低温干馏炉非常具有代表性,处理能力达到10万吨/年。SJ低温干馏炉是在鲁奇三段炉和现有内热式干馏炉的技术基础上,根据所在地及周边煤田的煤质特点而研制开发出的一种新型炉型,目前已在陕北榆林地区和内蒙古的东胜地区设计并建造超过500台SJ低温干馏炉,炉也由开始的SJ-Ⅰ发展到现在的SJ-Ⅶ。SJ干馏炉基本结构如图2-1所示。

图2-1 SJ干馏炉基本结构
1—进料口;2—排气桥管;3—炉顶煤仓;4—水封箱;5—炉体;6—气体混合器;7—排焦箱;8—排焦口;9—刮板输送机;10—熄焦池;11—推焦机;12—砖衬;13—喷火花墙;14—集气阵伞兼布料器;15—辅助煤仓
炉子截面:3000mm×5900mm,干馏段高(即花墙喷孔至阵伞边的距离)为7020mm,炉子有效容积91.1m3。距炉顶1.1m处设置集气阵伞,采用5条布气墙(4条完整花墙、2条半花墙),花墙总高3210mm。考虑花墙太高稳定性不好,除了用异型砖砌筑外,厚度也从350mm加大至590mm。花墙间距为590mm,中心距为1180mm。花墙顶部之间设置有小拱桥。干馏炉炉体采用黏土质异型砖和标准砖砌筑,硅酸铝纤维毡保温。采用工字钢护炉柱和护炉钢板结构,加强炉体强度并使炉体密封。
SJ低温干馏工艺基本原理是块煤经辅助煤箱和集气结构进入炭化室,经布气花墙均匀进入炭化室的高温废气逆向接触换热,逐段进行干燥和干馏,最后经排焦系统连续地排出。
单台年处理煤量10万吨SJ干馏炉主要工艺参数如表2-7所示。
表2-7 干馏炉主要工艺参数

物料和热量衡算见表2-8、表2-9。主要技术指标见表2-10。
表2-8 物料衡算表

表2-9 热量衡算表

表2-10 主要技术指标

2.2.1.2 SM-GF热解技术
该技术由陕煤集团与国电富通公司联合开发,属煤气热载体分段多层移动床热解工艺。热解炉为分段多层立式矩形炉,从上至下可分为干燥段(预热段)、干馏段和冷却段,每段由多层布气和集气装置组成,工艺流程如图2-2所示。原料煤首先进入干燥段,被来自冷却段的热烟气加热,脱除煤中水分,以减少热解工段酚氨废水的产出量,并将原煤加热至100~170℃;干燥煤进入热解段,被经蓄热式加热的自产高温富氢煤气加热到550~650℃,富氢气氛保证了系统较高的焦油收率;脱除大部分挥发分后的高温半焦进入冷却段,被来自干燥段的冷烟气降温,实现了干法熄焦;换热后的高温烟气被返送回干燥段加热原料煤,实现了半焦热量的回收。

图2-2 SM-GF热解工艺流程
1—煤斗;2—热解炉;3—旋风除尘器;4—直冷塔;5—横管冷却器;6—捕雾器;7—电捕焦油器;8—煤气风机;9—气柜;10—煤气加热炉;11—燃烧器;12—机械化澄清槽;13—重油罐;14—氨水槽;15—LAB水处理;16—轻油罐;17—集液槽;18—空气风机;19—烟气风机;20—水膜除尘器;21—布袋除尘;22—脱硫塔
陕煤集团陕北乾元能源化工有限公司,利用该技术已在榆林建成年处理煤量50万吨工业示范装置,以富氢煤气作为热载体,获取高品质热解产品,年产半焦31万吨、焦油4.5万吨、煤气7200万立方米,运行数据见表2-11~表2-16。
表2-11 原料煤分析(质量分数)

表2-12 长焰煤铝甑分析(650℃,质量分数)

表2-13 热解气组成(体积分数)

表2-14 产品煤气组分(体积分数)

表2-15 产品半焦分析

表2-16 产品焦油分析

2.2.1.3 DG热解技术
该技术由大连理工大学开发,将粒度小于6mm的原煤与800℃热半焦按一定比例快速混合热解,经分离净化得到低温焦油、煤气和半焦等产品。该技术主要由脉冲气流干燥预热、热烟气发生、热载体提升循环和混合热解系统组成,工艺过程见图2-3:以热解产生的高温半焦为热载体,与煤按一定的比例在混合器均匀、迅速混合,经混合器混匀的物料进入反应器,完成热解,由于物料粒度小,加热速度快,热解迅速析出气态产物;气态产物经净化除尘后进入焦油回收系统得到焦油和煤气两种产品;反应器部分固态产物半焦经给料器进入加热提升管,半焦与预热的空气进行热交换,使半焦达到热载体规定的温度,在提升管中被提升到一级旋风分离器,半焦与烟气分离;热半焦自一级旋风分离器入集合槽,作为热载体循环;烟气在二级旋风分离器除尘后外排。多余的半焦作为热解产物外送储存。

图2-3 DG热解技术工艺过程
陕煤集团神木富油能源科技公司采用该技术已建成年处理原煤60万吨的示范装置,年产半焦36万吨、焦油6万吨、煤气7900万立方米。以神木煤为原料,半焦、煤焦油、粗煤气特性分析数据见表2-17~表2-19。
表2-17 DG半焦特性分析

表2-18 DG煤焦油特性分析

表2-19 DG粗煤气特性分析

2.2.2 气流床热解工艺
2.2.2.1 SM-SP热解技术
SM-SP技术由陕煤集团上海胜帮科技股份有限公司开发,工艺过程如图2-4所示。装置分为煤提升进料、反应及粉焦冷却、烧炭及烟气综合利用、油气急冷及分馏单元。工艺采用10~100μm粉煤快速热解,反应过程中以循环煤气作载气,通过分馏技术分离制取轻焦油、中焦油、重焦油和煤气产品。工艺流程简介如下:粉煤经气力输送至原料存储单元后进入煤气循环管道,与循环煤气混合,再与粉焦热载体充分混合后进入热解反应器,粉煤在提升过程中与气固热载体充分换热,完成快速热解。热解产物进入气固分离单元分离粉焦,部分粉焦循环至热解反应器,其余粉焦进入粉焦冷却系统。气固分离后的热解气进入焦油回收单元,以自产焦油为吸收剂回收焦油,冷却净化后的煤气一部分作为循环煤气,一部分作为产品煤气输出界区。

图2-4 SM-SP工艺过程
陕西煤业化工集团利用该技术,正在建设年处理原煤120万吨的工业示范装置,之前已经完成年处理原煤2万吨的工业试验,焦油收率高达18.17%,油品重,芳烃、沥青质含量高,宜采用专门的加氢工艺生产市场紧缺的芳烃产品原料;煤气中有效气CO、H2、CH4总含量高达64.46%,碳二及以上各种烃类总含量21.22%,热值高达7920kcal/m3;粉焦含水0.19%,固定碳84.50%,平均粒径67.78μm,低位热值7178kcal/kg,适于作为气流床气化原料、高炉喷吹料、粉煤锅炉燃料等。
工业化试验数据见表2-20~表2-24:
表2-20 原料粉煤工业分析

表2-21 产品煤气成分(干基体积分数)

表2-22 粉焦性质(质量分数)

表2-23 焦油基本性质(质量分数)

表2-24 焦油族组成及馏程

2.2.2.2 输送床粉煤快速热解技术
该技术由西安建筑科技大学徐德龙院士团队和陕西煤业化工集团共同开发,主要由备煤、热解、气固分离、焦油回收、干法熄焦及余热回收等单元组成,工艺流程见图2-5。小于30mm的原煤经立磨磨制成平均粒径为200目的粉煤(水分<1%),熄焦后的氮气将粉煤预热后经加料器喂入热解反应器,然后被来自热风炉的高温气体快速加热,瞬间热解,产生气态产物和固体半焦,未反应完全的大颗粒经粗分离器返回热解反应器继续热解。热解反应器内气固同向流动,热解荒煤气经粗分离后,经深度除尘再进入焦油回收系统,回收焦油和煤气。高温高效分离单元分离出的半焦进入干法熄焦及余热回收系统,用循环氮气作为冷却介质,回收余热后的氮气显热用作粉煤预热的热量。

图2-5 输送床粉煤快速热解工艺流程
目前该技术已完成年处理原煤1万吨工业化试验,并进行了72小时现场考核,正在编制百万吨级工艺包。同时开展工业化示范项目建设前期准备工作。
2.2.3 流化床热解工艺
流化床热解工艺主要介绍浙大循环流化床热电多联产(ZD)工艺。
浙江大学在1985年由岑可法院士提出热电气多联产工艺设想,随后建立了1MW燃气蒸汽多联产试验装置,其工艺流程见图2-6。以循环流化床锅炉的高温循环热灰为热载体,将其送入用循环热煤气作流化介质的气化室内,气化室为常压鼓泡床。在气化室内循环热灰可将8mm以下的碎煤加热到750~800℃,发生部分气化。气化后的半焦随循环物料一起送回锅炉燃烧室内燃烧,产热发电,从而实现热电气联产。

图2-6 循环流化床热电气联产工艺
1—燃烧室;2—旋风分离器;3—返料阀;4—气化室;5—冷凝器;6—储气罐
红柳林煤1MW热解装置试验数据如下:
热解温度654℃,煤气产量0.11m3/kg煤,煤气密度0.78kg/m3,煤气产率8.5%,焦油产率9.98%,燃烧炉底渣含碳量约为0.78%,飞灰含碳量约3.4%,煤气成分见表2-25。
表2-25 煤气成分(体积分数)

浙江大学以循环流化床固体热载体供热的流化床热解技术为基础,与淮南矿业集团合作开发的12MW示范装置于2007年8月完成72h的试运行,获得了工业试验数据。该工艺的热解器为常压流化床,用水蒸气和再循环煤气为流化介质,运行温度为540~700℃,粒度为0~8mm的煤经给煤机送入热解气化室,热解所需要的热量由循环流化床锅炉来的高温循环灰提供(循环倍率20~30),热解后的半焦随循环灰送入循环流化床锅炉燃烧,燃烧温度为900~950℃。
12MW工业示范装置的典型结果为:热解器加煤量10.4t/h,焦油产量1.17t/h,煤气产量1910m3/h,煤气热值23.11MJ/m3,所得焦油中沥青质含量为53.53%~57.31%。
2.2.4 回转炉热解工艺
2.2.4.1 天元回转窑热解技术
该技术由陕煤集团神木天元化工公司和华陆工程科技公司共同研发,工艺流程见图2-7。将<30mm的粉煤通过回转反应器热解得到高热值煤气、煤焦油和提质煤。煤气进一步加工得到LPG(液化石油气)、LNG(液化天然气)、H2和燃料气;煤焦油供给煤焦油轻质化装置;提质煤达到无烟煤理化指标,可用于高炉喷吹、球团烧结和民用洁净煤。热解产品半焦达到高炉喷吹用无烟煤标准。煤焦油产率9.12%,热解煤气热值达6787.33kcal/m3,煤气中有效成分含量高于85%,其中CH4含量达39.59%、C2~C5含量达15.22%。

图2-7 天元回转窑热解技术工艺流程
该工艺技术特点有:①原料适用性强,适合≤30mm多种高挥发分煤种;②操作环境好,煤干燥、热解、冷却全密闭生产;③干燥水、热解水分级回收,减少了水资源消耗和污水处理量;④系统能效高,中试装置能效≥80%,工业化装置综合能效≥85%;⑤单系列设备原煤处理量大,单套装置规模可达60万~100万吨/a。
该项目总体规划了660万吨/a粉煤分质综合利用项目,目前正在进行60万吨/a示范。
2.2.4.2 龙成旋转床热解技术
该工艺由河南龙成集团研发,流程见图2-8。首先,通入氮气将炉窑中的空气进行置换,低阶原料煤从落煤塔通过皮带输送到受料缓冲仓,再经给料装置送入提质窑。气柜来的煤气经配风后进入提质窑内辐射管,经辐射传热间接与原料煤进行换热。原料煤在提质窑被加热到550℃提质后进入换能器冷却到约200℃,经喷水加湿降温后通过皮带输送到提质煤储仓。气体从提质窑中出来后经除尘进入冷鼓工段,回收其中的焦油。

图2-8 旋转床热解技术工艺流程
利用该技术,龙成集团在河北曹妃甸工业区建成了单套100万吨/a、总规模1000万吨/a的工业示范装置,洁净煤产率为61.65%,煤焦油产率为9.63%,煤气产量为126m3/t原煤。
2.2.4.3 三瑞外热式回转炉热解技术
该技术由西安三瑞实业有限公司研发,工艺流程见图2-9。成套装置主要组成部分包括:原料煤储运输送系统,粉煤干燥、热解、冷却回转炉,半焦干法熄焦及输送系统,煤气除尘、冷却、油气分离系统,焦油储罐,热风炉及高温烟气循环系统,煤气脱硫后处理系统,“三废”处理系统。

图2-9 三瑞外热式回转炉工艺流程
利用该技术,庆华集团于2013年建立了5万吨/a油砂热解示范项目,神华集团新疆公司于2014年建成15万吨煤热解制活性炭项目。
宏汇公司于2017年在甘肃酒钢建成单系列30万吨/a,总规模150万吨/a煤炭热解分质利用项目,其运行指标为:单炉进煤量42.3t/h,半焦产率50.50%,焦油产率11.49%,煤气产量120m3/t原煤。
2.2.5 旋转炉热解工艺
2.2.5.1 LCC热解工艺
该技术由大唐华银电力公司与中国五环工程有限公司联合开发,主要过程分为3步:干燥、轻度热解和精制,其基本原理是将煤干燥、煤干馏和半焦钝化技术相耦合,将含水量高、稳定性差和易自燃的低阶煤提质成为性质稳定的固体燃料(PMC)和高附加值的液体产品(PCT)两种新的能源化工产品。
工艺流程见图2-10。原料煤在干燥炉内被来自干燥热风炉的热气流加热脱除水分。在热解炉内,来自热解热风炉的热循环气流将干燥煤加热,煤发生轻度热解反应析出热解气态产物。在激冷盘中引入工艺水迅速终止热解反应,固体物料输送至精制塔,预冷却后与增湿空气发生氧化反应和水合反应得到固体产品PMC。

图2-10 LCC热解工艺流程
1—热解热风炉;2—干燥热风炉;3—烟气脱硫;4—干燥循环风机;5—干燥旋风除尘器;6—热解循环风机;7—干燥炉;8—热解炉;9—激冷盘;10—PCT静电捕集器;11—热解旋风除尘器;12—激冷塔;13—精制塔;14—PCT冷却器;15—激冷塔循环泵
从热解炉出来的气态产物经旋风除尘后进入激冷塔,塔顶出来的不凝气体进入电除雾器,气体中夹带的PCT被捕集下来,并回流至激冷塔。冷凝下来的PCT经换热器冷却后,大部分返回激冷塔,剩余部分为初步的PCT产品。从PCT静电捕集器出来的不凝气一部分作为热解炉的循环气体,剩余部分作为一次燃料。干燥炉出来的烟气经旋风除尘后大部分循环,小部分经脱硫后排放。
利用该技术,大唐华银电力公司在内蒙古锡林浩特市建成了年处理原煤30万吨的示范装置,运行期间煤焦油产率平均为3.05%,半焦产率平均49%左右,半焦发热量由原煤的3400kcal/kg提高到5900kcal/kg以上。
2.2.5.2 无热载体蓄热式热解工艺
该工艺由神雾集团开发,工艺流程如图2-11所示。蓄热式热解工艺由4个单元组成:原煤预处理单元、旋转床热解单元、油气冷却及油水分离单元以及熄焦单元。

图2-11 无热载体蓄热式旋转床干馏新技术流程
旋转床式干馏炉核心结构特征为环形移动床,粒度为10~80mm的原料煤经过预处理后,进入煤仓,通过布料装置装入旋转床干馏炉内,均匀铺放在炉底上部。炉底机械带动炉底连续转动,铺在炉底上部的料层随炉底转动,依次经过炉子的预热段、升温段和提质段,最终被加热到550~650℃完成干馏反应。高温油气从炉膛顶端或侧面多个出口快速排出,汇集后送往油气冷却系统和油水分离单元,由于油气在炉膛内停留时间很短,所以可以保证焦油的高产率。从油水分离罐分离出的高浓度污水送入污水焚烧系统焚烧或生化处理后作为制作水焦浆用水。半焦由出料装置卸出炉外,进入喷雾熄焦冷却装置进行冷却,热交换后的热蒸汽作为原料煤烘干或生产蒸汽的热源,冷却后的半焦输入焦仓。
该技术已建成3t/h的中试装置,焦油产率为9.79%,半焦产率72.06%,煤气产率11.06%,有效气组分超过82%。
2.2.6 带式炉热解工艺
带式炉由北京柯林斯达科技发展有限公司开发,以此为基础,陕西煤业化工集团联合柯林斯达公司开发了气化-低阶煤热解一体化(CGPS)技术。该技术是较早开展热解与气化过程耦合探索的技术之一,以粒煤(3~25mm)和成型粉煤(0~3mm)为原料,通过低阶煤的热解和粉焦或粉煤常压气化的有机耦合,在中低温条件下(500~800℃),将煤中有机挥发组分提取出来,制备煤焦油、半焦、热解煤气的成套新技术。充分利用了气化其显热,将其作为带式炉热解的热源,实现煤气化、热解两种工艺高效耦合,进一步提高整个系统的能源效率,热解气品质高,工艺流程如图2-12所示。

图2-12 气化-低阶煤热解一体化(CGPS)技术工艺流程
1—气化炉;2—分级布料器;3—热风炉;4—带式炉;5—冷凝水回收系统;6—油洗喷淋塔;7—油洗间冷塔;8—电捕焦油器;9—终冷器;10—除雾器
由备煤系统输送而来的原料煤经分级布料进入带式热解炉,依次经过干燥段、低温热解段、中温热解段和余热回收段得到清洁燃料半焦;干燥段湿烟气经冷凝水回收装置净化回收其中水分后外排;带式热解炉热源来自粉焦常压气化高温合成气显热,热解段煤层经气体热载体穿层热解产生荒煤气,荒煤气经焦油回收系统净化回收焦油后得到产品煤气,部分产品煤气返回带式炉余热回收段对炽热半焦进行冷却并回收其显热,随后进入气化炉与高温气化气调温后一起作为带式炉热解单元的气体热载体。
该技术已建成万吨级工业试验装置,热解炉进煤量1.25t/h,半焦产率57.84%,煤气产量309.17m3/t煤,干基焦油产率9.07%,煤气成分见表2-26。
表2-26 煤气成分(体积分数)

2.2.7 其他炉型热解工艺
这里主要介绍一种思路较为新颖的真空微波煤热解技术。该技术由西安龙华微波煤化工有限公司开发,利用OMCK-10型、装机容量75kW的真空微波煤热解试验炉,先后对块煤、粉煤、煤泥、焦炭泥煤、型焦煤球、油页岩、油砂、油渣等不同物料进行了热解试验,取得了大量数据。
该技术对进料煤种、粒度没有严格要求,适应范围宽;热心效应显著,急速加热,整体加热均匀;制得的半焦挥发分低,品质好。已建成了2万吨/年中试装置,真空微波炉功率450kW,热解温度500~650℃,压力-2500~-3000Pa,进煤粒度0~50mm,神木煤焦油产率大于18.2%,半焦产率65%(挥发分小于1%),煤气产量207.6m3/t,其中甲烷含量54.8%,低位热值6031.8kcal/m3。