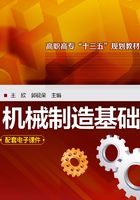
2.5 铸件结构工艺性
铸件结构工艺性是指铸件的结构应在满足使用要求的前提下,还要满足铸造性能和铸造工艺对铸件结构要求的一种特性。它是衡量铸件设计质量的一个重要方面。合理的铸件结构不仅能保证铸件质量,满足使用要求,而且工艺简单、生产率高、成本低。
2.5.1 铸造性能对铸件结构的要求
1.铸件壁厚要合理
在一定的工艺条件下,由于受铸造合金流动性的限制,能铸出的铸件壁厚有一个最小值。若实际壁厚小于它,就会产生浇不到、冷隔等缺陷。表2.5.1列出了在砂型铸造条件下常用铸造合金所允许的最小壁厚值。但是,铸件壁厚过大,铸件壁的中心冷却较慢,会使晶粒粗大,还容易引起缩孔、缩松缺陷,使铸件强度随壁厚增加而显著下降,因此,不能单纯用增加壁厚的方法提高铸件强度。通常采用加强肋(图2.5.1)或合理的截面结构(丁字形、工字形、槽形)满足薄壁铸件的强度要求。一般铸件的最大临界壁厚约为最小壁厚的三倍。
表2.5.1 在砂型铸造条件下铸件的最小壁厚值


图2.5.1 采用加强肋减小壁厚
2.铸件壁厚要均匀
铸件薄厚不均,必然在壁厚交接处形成金属聚集的热节而产生缩孔、缩松,并且由于冷却速度不同容易形成热应力和裂纹(图2.5.2)。确定铸件壁厚,应将加工余量考虑在内,有时加工余量会使壁厚增加而形成热节。

图2.5.2 铸件壁厚要均匀
3.铸件内壁应薄于外壁
铸件内壁和肋,散热条件较差,内壁薄于外壁,可使内、外壁均匀冷却,减小内应力,防止裂纹。内、外壁厚相差值约为10%~30%。
4.铸件壁连接要合理
为减少热节,防止缩孔,减少应力,防止裂纹,壁间连接应有铸造圆角(图2.5.3)。不同壁厚的连接应逐步过渡(图2.5.4),以防接头处热量聚集和应力集中。铸件上的肋或壁的连接应避免十字交叉和锐角连接(图2.5.5)。

图2.5.3 铸造圆角

图2.5.4 壁厚过渡形式

图2.5.5 铸件接头结构
5.避免铸件收缩受阻
如果铸件收缩受到阻碍,产生的内应力超过材料的抗拉强度时将产生裂纹。如图2.5.6所示手轮铸件,图2.5.6(a)为直条形偶数轮辐,在合金线收缩时手轮轮辐中产生的收缩力相互抗衡,容易出现裂纹。可改用奇数轮辐[图2.5.6(b)]或弯曲轮辐[图2.5.6(c)],这样可借助轮缘、轮毂和弯曲轮辐的微量变形自行减缓内应力,防止开裂。

图2.5.6 手轮轮辐的设计
6.防止铸件翘曲变形
细长形或平板类铸件在收缩时易产生翘曲变形。如图2.5.7所示,改不对称结构为对称结构或采用加强肋,提高其刚度,均可有效地防止铸件变形。

图2.5.7 防止铸件翘曲变形的结构
2.5.2 铸造工艺对铸件结构的要求
从工艺上考虑,铸件的结构设计,应有利于简化铸造工艺;有利于避免产生铸造缺陷;便于后续加工。注意以下几个方面:
1.铸件外形力求简单
在满足铸件使用要求的前提下,应尽量简化外形,减少分型面,以便造型。图2.5.8(a)所示端盖存在侧凹,需三箱造型或增加环状型芯。若改为图2.5.8(b)结构,可采用简单的两箱造型,造型过程大为简化。

图2.5.8 端盖铸件
图2.5.9(a)所示凸台通常采用活块(或外型芯)才能起模,若改为图2.5.9(b)所示结构,可以避免活块或型芯,造型简单。图2.5.10(a)所示铸件上的肋条使起模受阻,改为图2.5.10(b)所示结构后便可顺利地取出模样。

图2.5.9 凸台设计

图2.5.10 结构斜度的设计
2.铸件内腔设计
铸件内腔结构采用型芯来形成,使用型芯会增加材料消耗,且工艺复杂,成本提高,因此,设计铸件内腔时应尽量少用或不用型芯。图2.5.11(a)所示铸件,其内腔只能用型芯成形,若改为图2.5.11(b)所示结构,可用自带型芯成形。图2.5.12所示支架,用图2.5.12(b)所示的开式结构代替图2.5.12(a)所示的封闭结构,可省去型芯。在必须采用型芯的情况下,应尽量做到便于下芯、安装、固定以及排气和清理。如图2.5.13所示的轴承架铸件,图2.5.13(a)所示的结构需要两个型芯,其中大的型芯呈悬臂状态,需用芯撑支撑,若按图2.5.13(b)改为整体芯,其稳定性大大提高,排气通畅,清砂方便。

图2.5.11 铸件内腔设计

图2.5.12 支架

图2.5.13 轴承架
3.铸件的结构斜度
为了便于起模,垂直于分型面的非加工表面应设计结构斜度,图2.5.14(a)、(b)、(c)、(d)不带结构斜度不便起模,改为图2.5.14(e)、(f)、(g)、(h)较合理。

图2.5.14 结构斜度的设计