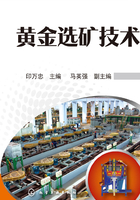
4.2 金的浮选特性和浮选分离方法
金的浮选包括自然金的浮选和含金矿石的浮选。在下列情况下,含金矿石有可能采用浮选法处理:
①金主要与硫化物结合;
②金虽然不是大部分与硫化物结合在一起,但后者能保证形成稳定的泡沫层;
③矿石不含有硫化物,但含有大量的氧化铁(如铁帽),这时赭石泥可起稳定泡沫的作用;
④矿石不含有硫化物或氧化铁,但含有能进入泡沫且能使泡沫稳定的矿物(如绢云母);
⑤纯的石英质金矿按一定比例预先与硫化物矿石混合,或选择适当的药剂以便能形成稳定的泡沫;
⑥用浮选法回收矿石中的主金属(铜、铅、锌等)后,尾矿进行氰化处理;
⑦砂金的浮选只适于从洗矿所得的产品中或其他较富的产物中浮出砂金。
大多数情况下,用浮选法处理含硫化矿物高的含金矿石可以把金最大限度地富集到硫化矿精矿中,并抛弃大量尾矿,从而降低冶炼成本;用浮选处理含多金属的金矿石时,能够有效地分离出金和各种有色金属的精矿,有利于实现对有价矿物资源的综合利用;对于不能直接使用混汞和氰化浸出的含金难处理矿石,需要采用包括浮选在内的联合流程进行处理。
4.2.1 自然金的浮游特性和浮选分离方法
金是一种易浮矿物,在原生的金矿床中,自然金常与黄铁矿、黄铜矿、方铅矿、闪锌矿、毒砂等硫化矿物共生。这些矿物同是易浮矿物,并能形成稳定的矿化泡沫,是金矿物最理想的载体矿物。通过浮选可以最大限度地使金富集到硫化物精矿中。自然金表面具有较好的疏水性,用黄药等硫化矿捕收剂均能浮选,载体浮选、离子浮选等微细粒浮选方法均可以回收微细粒级的自然金。
自然金的浮选具有以下特点:
①多数矿石中的自然金是以细粒浸染状存在,要使金粒达到单体解离必须细磨;
②金常与硫化矿物,特别是黄铁矿致密共生,因此回收金时需同时回收黄铁矿;
③金的相对密度很大,在浮选的过程中,金粒与气泡接触后易从气泡表面脱落;
④在氧化矿石中,金粒表面常被铁的氧化物所污染或覆盖;
⑤金具有柔性与延性,在磨矿时常呈片状,表面往往嵌进一层矿粒,使金粒表面粗糙。此外,钢球对金粒的研磨,金粒表面也会被金属铁颗粒所涂覆,例如用电磁铁从磨细的含金矿石中吸出金属铁颗粒(钢球研磨的产物)证明含有金。
金的粒度大小直接影响到它的可浮性,按粒度可分为四类:+0.8mm的金粒,不可浮;-0.8mm+0.4mm的金粒,难浮(只能浮出5%~6%);-0.4mm+0.25mm的金粒,可浮(浮出量约25%);-0.25mm的金粒,易浮(回收率可达96%)。可见,浮选的金粒不应大于0.4mm,故在浮选前需用重选、混汞或其他方法把粗粒金预先选出。
一般而言,金粒较细、可浮性好的硫化物含金石英脉矿石,含有多种有价金属(铜、铅和锌)的含金硫化矿石和含石墨矿石,都适宜采用浮选法回收。浮选法可以使金和其他金属硫化物富集到精矿中,并得到废弃尾矿。
由于金的密度很大,它虽然有很好的可浮性,由于数量少,不能形成稳定的矿化泡沫,仍然不能很好地浮游,金粒大于0.25mm及不含金属硫化物的石英岩含金矿石很难用浮选法回收。此时,可采用其他方法回收。
4.2.2 含金硫化矿的浮游特性和浮选分离方法
根据含金多金属硫化矿物的共生关系,含金矿石主要类型及伴生金属见表4-1。
表4-1 含金多金属硫化矿主要类型及伴生矿物

从表4-1所示,各种矿石类型中,金的伴生金属硫化矿物主要是黄铜矿及黄铁矿。
含金多金属硫化矿主要分为:含金铜硫矿石、含金铜铝锌矿石、锑金(砷)矿石、锑钨金矿石等。在含金多金属硫化矿中,粗粒的自然金一般常用重选法回收。但大部分自然金是以细粒浸染状赋存于黄铜矿、黄铁矿、毒砂、辉锑矿、方铅矿等硫化矿物中,它们紧密共生,有的还呈包裹体,在选矿过程中,金随着这些金属硫化矿物富集而富集,只能得到含金的铜、铅、锑、硫等硫化矿物精矿。含金硫精矿,如焦家、招远、新城、五龙、金厂峪、灵山、乳山等金矿选厂均采用氰化浸出提金;而龙水金矿选厂则采用硫脲浸出提金。以上两种方法的浸出渣均为硫精矿,作为生产硫酸的原料。其他含金硫化矿物精矿,只有在冶炼过程中加以综合回收金。
4.2.2.1 含金黄铁矿和毒砂的浮选分离方法
黄铁矿与毒砂的分离,对于处理含金砷硫化矿石具有重要意义。其分选原理是根据一些药剂如石灰、硫酸铜、无机氧化剂、氯化铵、有机抑制剂、碳酸盐对这两种矿物的选择性作用。黄铁矿与毒砂的分离方法有下列几种:
①用硫酸铜活化毒砂,在石灰介质中使之优先选为泡沫产物,而黄铁矿则留在槽内;
②在石灰介质中加入足够多的氯化铵抑制毒砂,浮出黄铁矿;
③采用无机氧化剂,或往矿浆中吹入氧使毒砂受到抑制,浮出黄铁矿;
④采用有机抑制剂选择性抑制毒砂,浮选黄铁矿;
⑤采用碳酸盐选择性活化黄铁矿,从而实现毒砂分离。
试验表明,若预先用硫化钠处理,接着把硫化钠完全排除,然后吹入氨,再用高锰酸盐或软锰矿氧化毒砂,则效果较佳。
下面详细介绍无机氧化剂抑制法、有机抑制剂抑制法和碳酸盐法。
(1)无机氧化剂抑制法 无机氧化剂种类很多,例如:氧气、高锰酸钾、双氧水、二氧化锰、漂白粉、过二硫酸钾、次氯酸钠、重铬酸钾等。一般认为,氧化剂加入浮选作业中,毒砂与黄铁矿的可浮性差异增大,毒砂的可浮性降低。氧化剂的作用是由于它们有助于在毒砂表面上形成臭葱石(FeAsO4·2H2O),从而抑制了毒砂。也有人认为,在氧化剂和碱存在的条件下,毒砂比含金黄铁矿更容易氧化,而且氧化程度、氧化速度和氧化产物均不相同。含金黄铁矿表面的氧化产物主要是,而毒砂表面的氧化产物除了部分
以外,更重要的是
。
容易溶解进入溶液,而
则吸附于毒砂表面,形成亲水膜,从而阻碍了毒砂表面与捕收剂的作用。还有人认为氧化剂用量、氧化时间和介质条件等对金砷分离有重要的影响。黄铁矿氧化以后,表面生成了元素硫,从而增强了其可浮性。
①高锰酸钾的氧化抑制方法 高锰酸钾比氧气更能降低毒砂的可浮性,而对黄铁矿的可浮性影响较小。适当浓度的高锰酸钾能够阻止黄铁矿表面氧化分解为硫化铁(FeS)和硫酸亚铁(FeSO4·7H2O)即水绿矾的形成,但却能够强烈地促进在毒砂表面形成臭葱石。有人认为,此时需要控制矿浆的氧化还原电位在400~500mV之间。采用二氧化锰5kg/t,在pH值为9时,抑制毒砂,其回收率仅为4.22%,说明毒砂被抑制的效果较好。
②过二硫酸钾的氧化抑制方法 使用过二硫酸钾氧化抑制毒砂,比使用大量的石灰或者高锰酸钾,或者在石灰的碱性介质中处理毒砂效果要好得多。过二硫酸钾是一种强氧化剂,与高锰酸钾相比,不仅抑制毒砂,而且活化黄铁矿,具有更长的最佳氧化时间,显示出极好的选择性。它在优先浮选中的特效与其双重性质有关,即过二硫酸钾与水相互作用,生成过一硫酸钾和硫酸钾,生成的过一硫酸钾同样产生硫酸钾和活性双氧水,反应如下:
因矿浆碱度为8.5左右,这一条件使双氧水分解并析出氧气,氧气与矿物(例如黄铜矿、黄铁矿、毒砂等)表面相互作用,产生适量的活性硫酸铜和元素硫,反应如下:
CuFeS2+4O2→CuSO4+FeSO4 (4-5)
4FeS2+11O2+6H2O→2FeSO4+4H2SO4+2Fe(OH)2+2S (4-6)
2FeAsS+7O2+6H2O→2(FeAsO4·2H2O)+2H2SO4 (4-7)
所以过二硫酸钾的加入,不仅可以抑制毒砂,而且还可以借助所生成的硫酸铜与矿物作用以及所生成的元素硫,活化黄铜矿和黄铁矿等矿物,使铜矿物和黄铁矿与毒砂实现最佳分选,从而提高金的回收率。
③加温氧化抑制方法 使用氧化剂作为抑制剂存在的主要问题是:当矿石中还原性物质很多时,其耗量大,不经济,因此加温搅拌抑制方法应运而生。该法可不用氧化剂,矿浆温度为40~50℃,碳酸钠调浆至pH值为7~9,并加以搅拌。某高硫高砷含金黄铁矿,原矿金品位为10g/t,砷以毒砂形式存在,品位为4.79%,硫和铁含量分别为33.73%和47.3%,经细磨的矿浆加温至45℃,搅拌0.5h,用丁黄药150g/t和2号油25g/t进行硫砷分选,经一粗三精,获得金硫混合精矿,其中砷为0.45%,硫为47.35%,金为23.05g/t,砷脱除率为97.22%。金硫混合精矿用石灰抑制黄铁矿浮金,浮选金硫后尾矿主要是磁黄铁矿和毒砂,弱磁选得合格磁硫铁矿精矿,磁选尾矿中的毒砂经硫酸铜活化,黄药捕收得金砷精矿。
需要指出的是:在采用上述三种氧化抑制方法的过程中,不仅要控制氧化剂的浓度,而且要控制好氧化时间、搅拌强度、搅拌时间以及矿浆温度等,否则不仅达不到理想的分选效果,而且还会恶化浮选过程。例如,搅拌时间的长短,不仅使矿物表面性质发生变化而影响其可浮性,而且还影响矿浆中的离子组成,而溶液中的离子组成对矿物的分选起着很大的作用,所以需要调整好搅拌时间,调节好矿浆中的离子组成,使之有利于下一步的分选作业。
(2)有机抑制剂抑制法 有机抑制剂价廉易得,而且无毒,例如糊精、苯胺染料、腐殖酸铵(钠)、丹宁、聚丙烯酰胺、木质素磺酸盐及其混合物,已经在金矿石浮选过程中得到应用,并且取得了满意的效果。
在分离毒砂和含金黄铁矿时,使用腐殖酸钠作抑制剂,能够消除重金属离子(例如Cu2+、Fe3+、Fe2+等)对含金黄铁矿和毒砂分选产生的不利影响。应用小分子抑制剂,发现HA23与未经Cu2+活化的毒砂表面发生化学反应,而与含金黄铁矿之间则没有这种反应。应用路易斯酸碱理论解释,认为HA23是属于硬碱类药剂,而毒砂是比含金黄铁矿稍硬的酸,硬酸对硬碱具有更强的亲和力,从而说明了HA23选择性地抑制毒砂的原因。HA24也有这种选择性地抑制毒砂的作用。他们还应用含有大量磺酸基和羟基等极性基团的大分子有机化合物S-711和L-339,发现在弱碱性介质中,均对毒砂有选择性地抑制作用,认为它们是以物理吸附的方式吸附于毒砂表面,因而产生抑制作用。此外,还利用烤胶以及烤胶与亚硫酸钠组合作抑制剂,它们对毒砂均有抑制效果,金精矿中砷含量分别为0.68%和0.41%。
采用腐殖酸钠(铵)作抑制剂时,能够选择性地抑制毒砂,而对黄铁矿的抑制作用较弱。应用高分子有机化合物YFA在碱性介质中抑制毒砂时,它表现出显著的选择性。此外,有人应用木质素磺酸盐抑制毒砂,为砷与硫化矿的分离提供了新途径。
研究表明,利用古尔胶、白雀树皮汁、木质素磺酸盐与硫酸锌、硫化钠等混合使用,能够更加有效地抑制毒砂。某矿山处理含金硫化矿时,使用燃料油作捕收剂,MIBC(甲基异丁基甲醇)为起泡剂,用白雀树皮汁抑制金与含金硫化铁,浮选碳质精矿(或丢弃或堆存),金的回收率总共可以达到86%。
(3)碳酸盐法 碳酸盐法包括碳酸钠和碳酸锌两种药剂。碳酸钠对黄铁矿表面的氧化产物有一定的清洗作用(溶解作用),从而活化黄铁矿,使黄铁矿和毒砂的可浮性差异增大,加强分选的效果。当联合使用碳酸钠和漂白粉时,可以强化对毒砂的抑制,而控制药剂的加药顺序,可以改善黄铁矿的浮选。使用碳酸钠作调整剂,要注意其用量,用量过高也会引起对金的抑制。氧化矿石的浮选,当需要在较高的pH值条件下浮选时,一般用碳酸钠的效果要优于石灰的效果,使介质pH值达到9左右,可溶性铁盐便产生沉淀。
在石灰介质中被抑制的黄铁矿,可以加碳酸钠或者硫酸加以活化。当矿石中存在黄铁矿和磁黄铁矿以及毒砂时,磁黄铁矿和毒砂的可浮性比黄铁矿的差,石灰对它们的抑制能力更强,加入适量的苏打,可以活化黄铁矿,实现与毒砂和磁黄铁矿的分离。
碳酸钠的活化作用,有人认为是由于它对矿浆pH值的缓冲作用和沉淀抑制Ca2+的作用所致。也有人认为加入碳酸钠,不仅可以调节pH值,而且使黄铁矿等矿物的表面负电位的绝对值增大,静电斥力势能增大,从而有利于矿粒的分散。据报道,适量的碳酸钠加入磨矿回路,对毒砂的浮选也具有良好的作用,原因是碳酸钠是金属铁的阻化剂,能使已溶氧在磨矿回路中保持在较高的浓度,这是在硫化矿物浮选之前使硫化矿氧化所必需的。另外,碳酸根离子既可以从已氧化的毒砂表面除掉砷,又能使其表面与捕收剂的阴离子继续作用。据此可以认为,碳酸钠溶液对于砷黄铁矿的优先浮选,可以被认为是浮选之前准备原矿的最好介质。俄罗斯一选矿厂采用这一制备浮选矿浆的方法处理金-砷矿石,使毒砂的回收率提高13.20%、金回收率提高5.5%。
碳酸锌法实质上是胶体碳酸锌法。如果单独使用碳酸钠,其对毒砂的抑制作用较弱,单独使用碳酸锌对毒砂基本无抑制作用。但是,当硫酸锌与碳酸钠以一定比例混合配制成胶体碳酸锌作抑制剂时,却能够满意地抑制毒砂的浮选。同时发现:不论碳酸钠和硫酸锌的配比如何,使用胶体碳酸锌对含金黄铁矿的可浮性没有影响。碳酸钠和硫酸锌的合适配比应以硫酸锌含量在30%以下比较适宜,此时抑制毒砂的效果较好。
4.2.2.2 含金黄铁矿的矿浆电位控制浮选法
含金硫化矿的浮选实质上是浮选载金矿物例如黄铁矿、黄铜矿、毒砂、方铅矿等以及部分呈游离状态的自然金。在此过程中,研究发现矿浆电位Eh起着非常重要的作用。捕收剂诸如黄药、黑药或者这两种药剂的混合物在阳极形成硫化矿物的疏水膜,该阳极过程与阴极过程例如氧的还原相互陪伴,使得浮选回收率与矿浆电位紧密地联系在一起。
除了可以通过矿浆中的氧气控制电位外,还可以采用化学药剂控制电位。所用的药剂一般有硫化钠、连二亚硫酸钠、二氧化硫和过氧化氢等。化学药剂控制电位的不足之处是药剂耗量可能较高,会有化学副作用,使矿物表面发生不利于浮选过程的反应,或者使捕收剂发生分解。此外,由于矿浆中存在溶解氧,会消耗过量的还原剂。
(1)含金黄铁矿浮选过程中矿浆电位的作用 硫化矿选厂一般是将矿浆电位控制在+100mV到-300mV之间,并由空气设定。在充空气时,这个矿浆电位范围对于最佳的回收率而言通常是过氧化的。过氧化使矿物浮选选择性降低,这可能是由于容易氧化的矿物(例如毒砂和磁黄铁矿等)氧化生成的产物所致。这些反应产物的溶解和不加选择地吸附在矿浆中不同矿物的表面,从而造成浮选过程的无选择性。此外,氧化反应生成的元素硫、金属氢氧化物、硫代硫酸盐以及其他表面层的形成,也可能是浮选过程选择性降低的原因。所以为了防止过氧化现象的发生,还原剂的使用是必要的,以便将矿浆控制在合适的电位范围内。
矿浆的电位控制还与磨矿过程紧密相关。磨矿过程的电位较低,特别是在标准的钢磨机中,所以需要采用电位调整剂来控制,以便提高磨矿过程的电位,使硫化矿物或者含金硫化矿物达到较高的浮选回收率。
矿浆电位在浮选过程中起着非常重要的作用。对它的研究和应用极大地丰富了浮选理论和应用的内容,使其成为浮选研究的重要分支学科之一。
(2)含金黄铁矿的可浮性与矿浆电位的关系 黄铁矿的浮游需要以下条件:
①有可供利用的黄铁矿氧化产物,黄铁矿的氧化产物可由粗粒上产生,并且具有可溶性,可以产生酸性氧化条件;
②需要有其他硫化矿物(诸如黄铜矿和方铅矿)中的一种存在,以便产生诱导浮选现象;
③在含有Fe2+的溶液中,可以通过添加配合剂或者提高矿浆的pH值,或者通过这两种方法来形成还原阶段;
④添加配合剂,可以使金属氢氧化物的沉淀减至最少程度,使硫化矿物表面的亲水性物质除去而获得纯疏水特性;
⑤在浮选阶段建立起足以发生氧化作用的矿浆电位。
此外,无铜离子存在时,黄铁矿的回收率较低。如果这5个条件得到满足的话,则铜离子可以大幅度地提高黄铁矿的回收率;如果这5个条件中的任何一个都不满足的话,则黄铁矿不具有可浮性。对于复合矿石或者实际矿石而言,除螯合剂、配合剂外,其他几个条件都是满足的。
由以上5个条件可知,含金黄铁矿的可浮性与矿浆电位紧密相关。研究发现,当矿浆电位Eh为-250mV时,辉铜矿开始上浮,而当Eh为-50mV时,其浮选回收率可达100%;辉铜矿的浮选回收率和黄药的吸附密度之间有较好的对应关系。而黄铁矿在矿浆电位为50mV时开始上浮,在Eh为320mV时,其回收率可达100%;同辉铜矿一样,黄铁矿的黄药吸附密度与其回收率之间也有一个很好的对应关系,不同之处在于,黄药吸附密度下降,这可能是因为形成了一种称为过黄药的新物质,此外,浮选矿浆电位增大,与双黄药的形成有关。
但当黄铁矿和辉铜矿混合存在时,黄铁矿的上浮矿浆电位Eh范围为-150~150mV,混合矿中辉铜矿的上浮与单一的辉铜矿相比,发生在相似的矿浆电位范围内,但是有不同程度的抑制。
(3)含金黄铁矿抑制的电化学机理 通过对硫化矿物的电化学浮选研究,OH-抑制黄铁矿浮选的电化学机理如下。
①由于黄药氧化为双黄药的过程中没有OH-或者H+参加反应,所以矿浆pH值对黄药在黄铁矿表面上的氧化动力学几乎没有影响。
②随着矿浆pH值的增大,黄铁矿自身的氧化速度加快。在较小的阳极电位和较高的pH值条件下,黄铁矿就出现了氧化电流。当pH值为11.4时,黄铁矿开始氧化的电位比黄药在黄铁矿表面氧化为双黄药的电位小。
③当pH值小于11.4时,黄铁矿的氧化电位大于黄药在黄铁矿表面的氧化电位,即黄药氧化为双黄药的反应优先发生,氧气将在阴极被还原,OH-不起抑制作用,黄铁矿可浮。当pH值大于11.4时,将优先发生黄铁矿的自身氧化,这样在黄铁矿表面不仅不会形成疏水膜,而且亲水性更大,从而阻碍了黄原酸根离子氧化为双黄药以及黄铁矿的浮选,有关反应如下:
(4)含金黄铁矿的无捕收剂浮选 含金硫化矿的无捕收剂浮选是在含金硫化矿物电化学调控下捕收剂浮选的基础上发展起来的新的研究领域,它是充分利用硫化矿物自身的结构特征,依据电化学原理,通过调整矿浆电位,来控制浮选体系的氧化还原性质,使矿物表面形成非捕收剂的疏水化,从而实现矿物的彼此分离。
世界上许多金矿石的选矿,一般来说以浮选以及浮选与氰化浸金的联合流程为主。我国现有的黄金企业中,据统计,采用单一浮选作业或者与其他选冶相结合的流程大概有70%以上,其浮选所得金精矿仍需要进一步湿法或者火法冶金技术处理。综观国内外的选矿实践,不论是对于以金为主的单一金矿石的浮选,还是对于以硫化矿为主的伴生金矿石的浮选,都不可避免地使用浮选捕收剂、抑制剂、起泡剂甚至活化剂等,同时,这些药剂特别是捕收剂(诸如黄药、黑药等试剂)的用量大,成本高,作业加药点多,管理复杂,金精矿的脱药效率低,残余的黄药和二号油或者MIBC等仍然较多,从而影响下一步的氰化浸金作业效果。这也是目前国内外金矿石浮选-氰化浸金工艺普遍存在的问题。
因此,开展含金硫化矿特别是与金关系密切的黄铁矿、黄铜矿等硫化矿物的无捕收剂浮选研究,对于降低生产成本、避免金精矿浸金前的脱药工序、便于生产管理、提高后续氰化浸金作业金的回收率等,具有十分重要的理论价值和实际意义。
近年来,国内外许多科技工作者应用现代电化学原理和测试技术、手段,从硫化矿浮选体系的氧化还原性质出发,将硫化矿物的浮游行为与矿浆的电位联系起来,使浮选过程更加便于控制和自动化,这也为含金硫化矿无捕收剂浮选的研究和应用的成功提供了可能性和现实性。国内外的研究结果表明:硫化矿物的无捕收剂浮选不仅可以实现,而且与常规而又传统的黄药类捕收剂泡沫浮选技术相比,具有更好的选择性、更加简单的浮选药剂制度以及更高的精矿质量。
常见的硫化矿物,诸如黄铜矿、方铅矿和黄铁矿等都具有良好的电子导电性,这些硫化矿由于其表面结构特征、表面电子状态以及电子传导能力等的不同,使得它们实现无捕收剂浮选的途径也不相同。
硫化矿物的无捕收剂浮选可以大致地分为两类:一类是以方铅矿、黄铜矿为代表的硫化矿物在电化学调控下,自身的氧化就可以导致矿物表面的无捕收剂疏水化和浮选,它们可以借助于电化学调控技术,使其表面硫上的电子转移给电负性较大的分子氧,而被氧化成元素硫(S0)或者富硫层(M1-zS),这二者疏水性好,可以使黄铜矿和方铅矿表面疏水化,所以它们表面硫的自身氧化生成的元素硫或者富硫层是其无捕收剂浮选的主要疏水体,故黄铜矿等具有良好的无捕收剂无硫化钠浮选行为。黄铜矿等硫化矿物在酸性和碱性条件下都可以在其表面生成元素硫(S0),反应式如下:
CuFeS2+3H2O→CuS+Fe(OH)3+S0+3H++3e (4-9)
CuFeS2→CuS+Fe2++S0+2e (4-10)
富硫层是硫化矿物初期氧化、金属离子部分离开其表面而形成的一层金属少、硫多的非化学计量层,富硫层形成的可能化学反应如下:
MS+zH2O→M1-zS+zMO+2zH++2ze (4-11)
硫化矿物无捕收剂浮选的另一类是以与黄铜矿等表面电子状态不同的黄铁矿为典型代表,黄铁矿不具备自身氧化而生成元素硫或者富硫层的能力,不能无其他化学试剂疏水化和浮选,需要外加硫离子(S2-),确切地说是外加硫化钠,通过硫化钠在矿物表面上的氧化,导致硫化矿物的无捕收剂疏水化和浮选。
当硫化钠加入矿浆以后,会解离出HS-和S2-,S2-和HS-上的电子可以通过黄铁矿表面上的硫质点传递给分子氧,这样的电子转移将导致溶液中的S2-和HS-氧化为元素硫或者富硫层,并覆盖在黄铁矿表面,促使其疏水化而浮选。在该过程中,阳极的氧化反应和相应阴极的还原反应分别如下所示。
阳极: HS-→S0+H++2e(E0=-0.065V) (4-13)
S2-→S0+2e (E0=-0.48V) (4-14)
由于阳极失去电子和阴极得到电子是通过黄铁矿表面传导电子实现的,所以可以形象地表示如下:
黄铁矿表面:
H++S0+2e←HS- (4-16)
国外对于黄铜矿、黄铁矿、方铅矿和闪锌矿的单一矿物中等碱性条件下,无捕收剂无硫化钠的自感应性浮选试验研究表明,黄铜矿和方铅矿的较好可浮性以及黄铁矿和闪锌矿无捕收剂时的很差可浮性试验结果,与上述的分类结果一致。对于黄铁矿和石英的混合物,研究表明:在pH值为8或9时,黄铁矿不具有无捕收剂浮选的条件。此时不论是铜盐、铅盐还是过量的乙二胺四乙酸盐,均不能促进黄铁矿的浮选。所以乙二胺四乙酸盐这一配合剂不能从黄铁矿-石英的混合物中从黄铁矿表面上剥离金属离子或者金属氢氧化物,使其表面成为富含硫的疏水层。
在硫化钠存在的条件下,在pH值为8或9时,硫化后的黄铁矿可以实现无捕收剂浮选,回收率可达90%以上。
研究还发现,在黄铁矿与方铅矿和闪锌矿的混合物以及与黄铜矿和石英的混合物中,黄铁矿可以与黄铜矿和方铅矿在中等碱性条件下,一同实现无捕收剂上浮。但是,当黄铁矿与闪锌矿和石英一起时,则黄铁矿并不可浮。导致黄铁矿在中等碱性条件下浮游的疏水性本体是以硫为基础的物质,它来自另一种硫化矿物(例如黄铜矿或者方铅矿)。造成硫由其他硫化矿物向黄铁矿表面转移的中介物可能是某种可溶性硫化物,并且这个过程矿浆的pH值和电位(Eh)紧密相关。
4.2.2.3 含金铜硫硫化矿石的浮选方法
含金铜硫硫化矿石较多,自然金大部分呈细粒赋存于黄铜矿、黄铁矿中,常采用优先或混合浮选工艺流程,在分离时,加入石灰来抑制黄铁矿,浮选硫化铜矿物,得到合格的含金铜、硫精矿。
4.2.2.4 含金铜铅锌硫化矿石的浮选方法
含金铜铅锌硫化矿石,一般采用铜铅部分混合浮选工艺,再将铜沿混合精矿进行分离,得到铜、铅精矿,金常富集在铜精矿中。有的铜铅混合精矿,由于铜、铅硫化矿物可浮性相近,共生关系比较复杂,难以浮选分离,得不到合格的含金铜、铅精矿。可将含金铜铅混合精矿,采用碳酸化转化-浮选法提金,使铜铅得到分离,综合回收金、银等贵重金属。
4.2.2.5 含金铜铁矿石的浮选方法
含金铜铁矿石,主要矿物是黄铜矿及磁铁矿,而自然金呈微细粒赋存于黄铜矿中,可用浮选-磁选联合工艺流程来进行处理,分别得到含金铜精矿和铁精矿等两种产品。
4.2.2.6 含有硫化矿的含金石英脉矿石的浮选方法
浮选含有硫化矿的含金石英脉矿石时,可采用乙基或丁基黄药作捕收剂进行混合浮选,而对于稍受氧化的矿石则宜采用戊基黄药进行浮选,也可采用某种烃基二硫代磷酸盐作为辅助捕收剂。
4.2.2.7 含金黄铁矿和磁黄铁矿的浮选分离方法
含金黄铁矿与磁黄铁矿的分离可往矿浆中强烈吹入空气,用石灰抑制这两种矿物,然后用苏打选择性地活化黄铁矿,磁黄铁矿氧化时,表面迅速形成一层牢固的亲水氧化膜,而黄铁矿表面形成的亲水氧化膜在苏打介质中则被清洗,因其所生成的碳酸盐易从表面脱落下来。
4.2.2.8 含砷金矿石的浮选方法
含砷金矿石的处理,基本上可以归纳为两种方法:①含砷量低而且毒砂中含金较少的矿石,用浮选方法脱砷,得到合格的含金黄铁矿精矿,再进一步提金;②含砷较高而且毒砂中含金较高的矿石,通过浮选得到含砷金精矿和含硫金精矿,再按相应的工艺流程脱砷提金。
4.2.3 含金氧化矿的浮游特性和浮选分离方法
含金氧化矿石明显地与硫化矿不同,氧化矿一般距离地表10~30m的范围,储量不大,矿体比较分散。由于矿物和金粒表面蚀变、氧化和污染,使其失去原来的可浮性。另外,由于微细粒矿泥(原生矿泥和次生矿泥)含量大,微细粒矿物质量小,比表面大,表面能亦大,使得水介质对这些微细粒矿物和矿泥的动阻力、各种界面力、双电层斥力等的影响越益显著,布朗运动扩散行为的影响远远超过重力的作用,使得它们与气泡碰撞黏附的几率降低,泡沫发黏,比浮选速度小;有时大量矿泥进入精矿,造成金精矿品位过低。此外,矿泥和微细矿粒还吸附浮选药剂和显微、次显微金。这些都导致浮选过程的复杂化,增加生产成本,降低选矿回收率。所以,直接采用浮选法处理含金氧化矿,金的浮选回收率一般只有60%左右,精矿品位也不高,甚至达不到金精矿标准。如果采用混汞-重选工艺流程处理,金的回收率也只能达到60%~70%,同时,重选尾矿再进行氰化,回收率虽然能够大幅度提高,但工艺流程复杂,环保问题也难以解决,对于中小型黄金企业来说,经济上也不合算。
4.2.4 含锑金矿石的浮游特性和浮选分离方法
在锑金(砷)硫化矿石中,主要目的矿物有辉锑矿、自然金、黄铁矿、毒砂等,而黄铁矿、毒砂是主要载金矿物,有的辉锑矿也含金。毒砂含砷,有时黄铁矿也含砷。因此,这类型矿石含砷较高。
该类型矿石中的锑金(砷)分离,除了粗粒自然金用重选回收外,但大部分是辉锑矿与黄铁矿、毒砂等矿物的分离。浮选分离锑金(砷)矿物的工艺流程在实践中有优先浮选及混合-优先浮选。浮选分离的方法有下列几种:氢氧化钠法;硫化钠-氢氧化钠或碳酸钠法;氧化剂法;丁铵黑药法;氰化物法。因氰化物有毒,影响环保,并溶解金、银,该法在国内目前应用较少。
(1)氢氧化钠法 采用优先浮选工艺流程,在球磨机中加入氢氧化钠,在强碱性矿浆中磨矿来抑制辉锑矿,用硫酸铜来活化黄铁矿及毒砂,再将矿浆pH值调到8~9,加入捕收剂及起泡剂,浮选出黄铁矿及毒砂,得金(砷)精矿,其尾矿加入铅盐或铜盐活化辉锑矿,再加入捕收剂及起泡剂进行浮选,得锑精矿。
(2)硫化钠-氢氧化钠或碳酸钠法 在磨矿过程中加氢氧化钠及碳酸钠,然后加醋酸铅、硫酸铜、丁基黄原酸钠(丁基黄药)及硫酸进行混合浮选得锑金混合精矿与废弃尾矿。混合精矿经再磨,磨矿时加氢氧化钠、丁基黄药、硫酸铜并充气几分钟,然后进行浮选分离,得金粗精矿,槽中产物就是锑精矿。再将金粗精矿采用硫化钠-氢氧化钠法来抑制辉锑矿进行精选,得到金精矿及低品位锑精矿。
(3)氧化剂法 在混合精矿浮选分离前,加入氧化剂漂白粉(CaOCl2)或高锰酸钾(KMnO4),矿浆固:液=1:3,搅拌时间为1min,然后加入醋酸铅100g/t,用黄药为捕收剂来浮选辉锑矿。其尾矿为含金黄铁矿精矿。
(4)丁铵黑药法 利用丁铵黑药对辉锑矿捕收能力较强、具有较好的选择性,而对毒砂及黄铁矿捕收能力弱的特点进行锑金(砷)浮选分离的一种方法。先在磨矿-分级回路中用捕金器或重选即时选出粗粒单体自然金。然后采用优先浮选流程,用铅盐作辉锑矿的活化剂,以硫酸来调节矿浆的pH值,丁铵黑药为捕收剂,松醇油为起泡剂,在自然pH或弱酸性矿浆中浮选出辉锑矿得锑精矿。浮选尾矿就是含金毒砂(黄铁矿)粗精矿(因丁铵黑药对毒砂捕收能力弱)。将其尾矿加入丁基黄药,必要时加硫酸铜活化,再加起泡剂浮选出含金毒砂精矿,并从中提取金。锑精矿中的金,在冶炼锑的过程中进行综合回收。
(5)锑金多金属硫化矿物的浮选分离方法 锑金多金属硫化矿石产于中低温热液裂隙充填锑金共生矿床,主要矿物为辉锑矿,其次为自然金、硫锑铅矿、锑的氧化物、黄铜矿、黄铁矿、毒砂等。脉石矿物主要有石英,其次为绢云母、硅酸盐等。辉锑矿多为致密块状。自然金呈不规则微粒状,金与毒砂紧密共生。
一般采用混合-优先浮选流程,如图4-4所示。将矿石磨到-0.074mm为60%~80%。先混合浮选锑金(砷),得混合精矿,然后进行锑金(砷)浮选分离,采用硫化钠-碳酸钠法来抑制辉锑矿,浮选金(砷),经两次精选得金(砷)精矿,槽内产物为锑精矿;混合浮选的尾矿经扫选,扫选的泡沫产物给入锑金(砷)浮选分离系统,槽内产物再经过一次锑粗选、一次精选、一次扫选,得成品锑精矿和废弃尾矿,中矿返回锑金(砷)混合浮选的扫选作业。

图4-4 锑金多金属硫化矿物的浮选分离工艺
浮选药剂:在锑金(砷)混合浮选时,矿浆pH值调整为6.5,以黄药和黑药为混合捕收剂,硝酸铅和硫酸铜为混合活化剂;在锑金(砷)浮选分离时,矿浆pH值调整为11~12,加入硫化钠和碳酸钠调整剂。
青海某金矿石属少硫化物石英斑岩型微细浸染状含锑金矿山,金粒度小于0.005mm,主要包裹在硅酸盐、碳酸盐及硫化物中,有害元素砷含量较高。采用直接氰化、焙烧-氰化试验浸出率均较低。针对该矿石性质,孙晓华等采用细磨-锑金优先浮选-金精矿抑砷浮选处理工艺。锑、金分别经过两次粗选、两次扫选、两次精选,可获得锑品位57%,回收率62.7%的锑精矿;金品位32.35g/t,回收率73.28%的金精矿。
4.2.5 含石墨或炭质页岩金矿石浮游特性和浮选分离方法
金矿中含石墨或炭质页岩,会使浮选和金的提取过程复杂化。据估计,此类矿石约占全世界金矿的4%,属难选金矿。石墨进入金精矿后,在氰化过程中,它就会像贵金属的沉淀剂那样,从氰化溶液中将金沉积出来,并损失于氰化尾矿中。如果石墨在矿石中是以单独颗粒存在,不含有价的金,则可加起泡剂除去,若石墨呈极细粒存在于整个矿石中,这将会给分选和氰化带来相当大的困难。